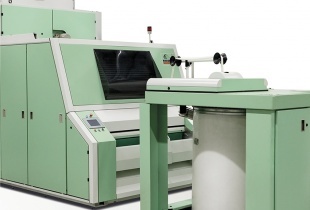
Card-C701
|
Top quality & productivity
- Carding surface of 3.74 sqm for: a thinner layer of material on the main cylinder, a lower carding density (i.e. number of fibers per point) and, consequently, higher production and quality performances
- Working width of the main cylinder of 1,500 mm in order to reach a high carding surface with a smaller diameter. This allows to reduce the peripheral speed of the raw material on the main cylinder and consequently avoid excessive stress on the fibers and wear of the carding flats
- 90 movable flats. 32 always in working position to guarantee the highest carding performances
- Fully integrated chute feed that ensures that the batt is perfectly even and that is made of small and more open tufts
- Small taker in (256 mm) rotating at higher speed (up to 1,500 rpm) to achieve a higher centrifugal force and, consequently, an easy elimination of trash
- MTA (medium-short) autoleveller in order to ensure the evenness of the card sliver
- Pre carding area with 6 carding units and 2 fiber control units with relative knives and post carding area with 4 carding units and 2 fiber control units with relative knives for excellent cleaning from impurities, dust and short fibers
- Minimum mechanical distance between doffer and main cylinder and big diameter of the doffer (700 mm) to allow an easier transfer of the fibers
- Casting structure for reliable settings of the machine: no variations of the settings (e.g. flats settings, distance between doffer and main cylinder) caused by temperature changes
- Constant quality control of the sliver in the last area of compaction
Higher efficiency
- Higher production volumes allow to reach leading Kw/Kg ratios
- Specifically-designed suction system for the 1,500 mm working width to ensure excellent removal of impurities while containing the amount and pressure of the air
User friendliness
- Modern PC microprocessor to manage the machine and multi-language touch screen
- Special design of the external covers to grant high accessibility, mobility and visibility for maintenance personnel
Technical Data:
Processed fibers |
Cotton, man made fibers and wool with staple length up to 65 mm |
Production |
Up to 270 Kg/h |
Carding surface |
3.74 sqm |
Main cylinder width |
1,500 mm |
Main cylinder diameter |
1,006 mm |
Carding angle |
284° |
Moving flats |
90 of wich 32 always working |
Pre carding |
up to 8 carding unit |
Post carding |
up to 6 carding unit |
Licker-in diameter |
256 mm |
Doffer diameter |
700 mm |
Delivered silver count |
Ktex 3 - 30 |
SKU : SKUC701
Category : CARDING SECTION
Datasheet :
PDS_C701_r3-min.pdf
Tags :